コンサルティング
機器設置
設計施工
その他
某電子工場F社様
電子
排ガスソリューション
3Rソリューション
洗浄に使用するフッ素系洗浄剤の年間のランニングコストを大幅削減
洗浄工程で使用されるフッ素系洗浄剤のガスをREARTH導入により液化回収した。回収したフッ素系洗浄剤を再利用することで新液購入量を大幅削減できた。
お持ちの課題
ご相談内容
高価なフッ素系洗浄剤を用いて精密部品の洗浄を行っているが、ランニングコストが高く、廃液の再生以外でさらにコストダウンできる方法を探していた。
課題発生時の状況
電子デバイス製造工程において、生産量が安定的に多い部材を製造しており、洗浄プロセスに置いて使用しているフッ素系洗浄剤の使用量が非常に多く、ランニングコストを圧迫していた。また同様のラインが複数あり、可能であれば複数ラインを一度に対応ができる方法を調査していた。
【フッ素系洗浄剤新液】
購入量:150L/日/2ライン
購入金額:1,200,000円/日/2ライン
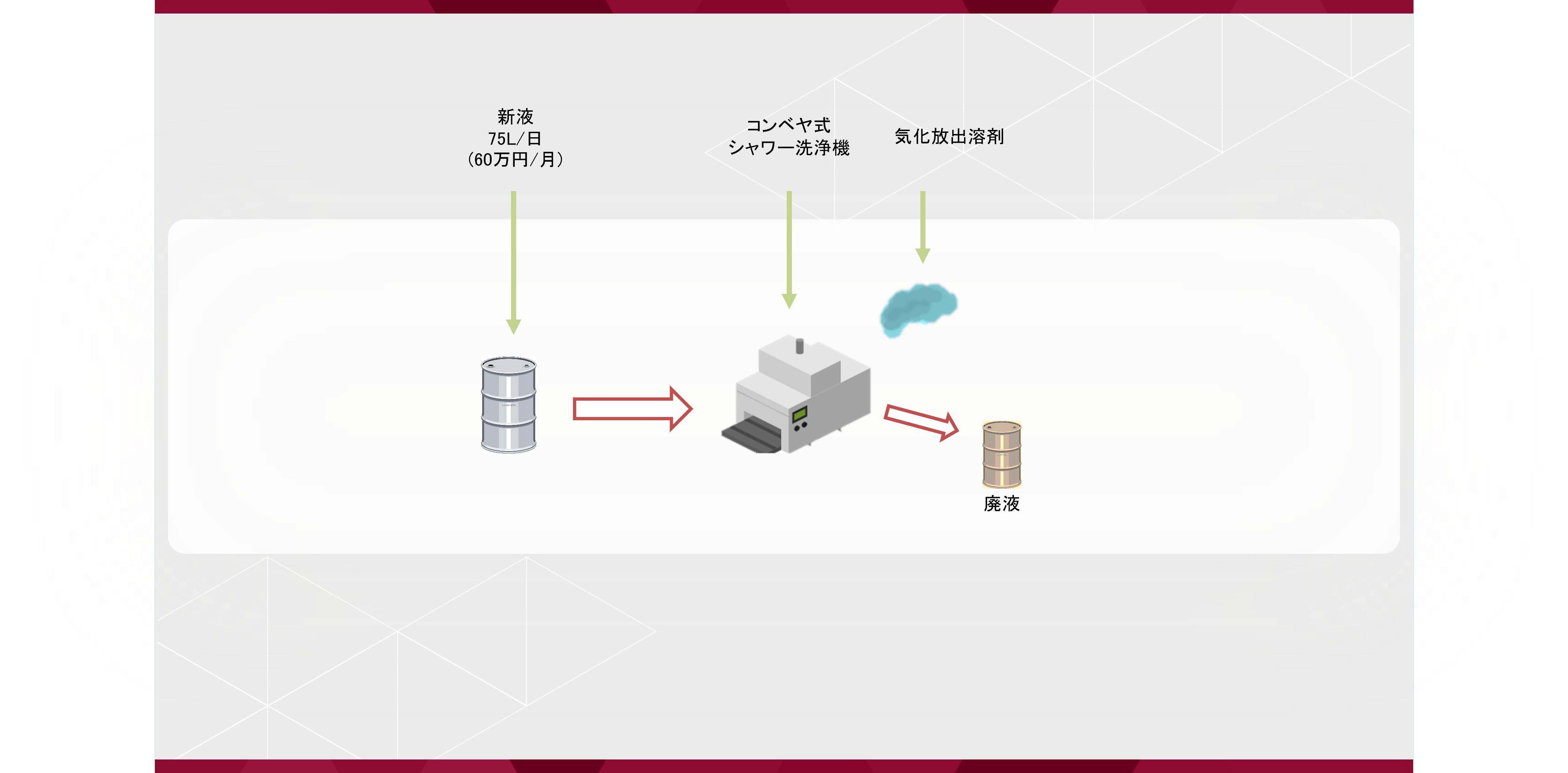
現状から導かれた初期仮説
廃液はすでに蒸留再生を行っていたが、新液投入量と廃液発生量のマテリアルバランスがズレており、ガスが余計に漏洩している可能性が高かった。放散されているガスを液化回収ができればコストダウンにつながる可能性があった。
解決への取り組み
独自の圧縮深冷凝縮方式を持つ揮発ガス回収システムREARTHを導入した。回収液から水分値を下げるため水分離工程を導入した。対象として2ラインを同時に対応することとした。
疑似ガス吸引フローを設け、吸引デモ試験を行い、REARTH導入後の揮発ガス回収率の効果検証を行った。放散ガスは平均22,750ppm程度が検知されたため、150L/min×24hrの条件にて2ライン合計で50.3kg/日の回収が見込めることがわかった。ただし、回収液には洗浄剤に含まれるアルコール成分に溶解している水分も同時に回収されてしまうため、水分離ユニットを設け、再利用性を向上させることとした。
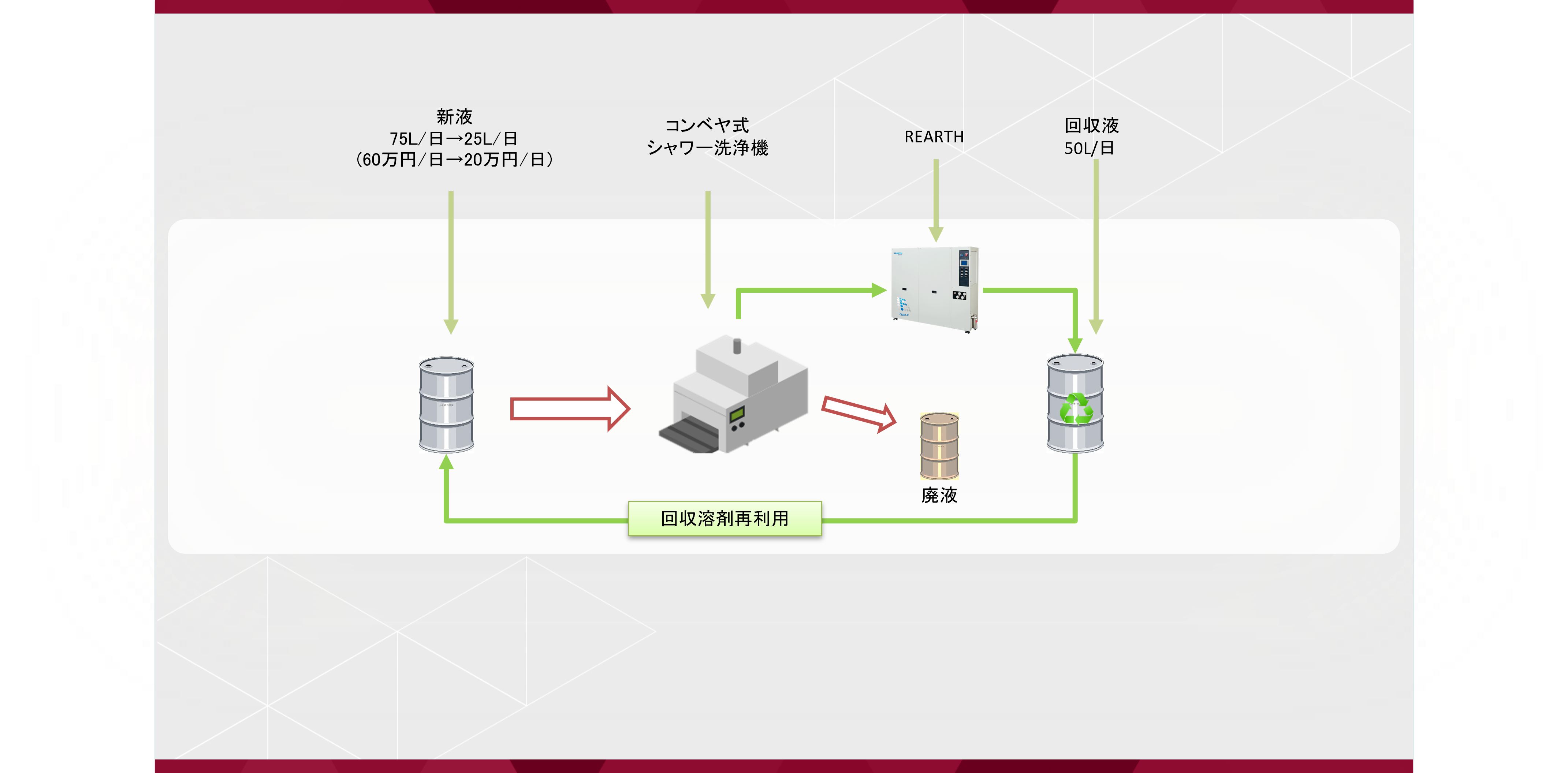
得られた成果
揮発ガスの回収再利用によりコストダウンを実現
REARTHと水分離ユニットの導入により、揮発分のフッ素系洗浄剤を30%以上液化回収できるようになった。
対応前
【フッ素系洗浄剤新液】
Before | |
---|---|
購入量 | 150L/日/2ライン |
購入金額 | 1,200,000円/日/2ライン |
対応後
【フッ素系洗浄剤新液】
After | |
---|---|
購入量 | 100L/日/2ライン |
購入金額 | 800,000円/日/2ライン |
非常に高いコストダウン効果が得られて満足している。他の製造ラインがあるため、追加購入を検討している。
NAGASEのコンサルタントから
コメント
コメント
クリーンルーム内でのガス回収案件のため、導入完了まで様々なハードルがあったが、お客様ご担当者様が導入後の効果を見て非常に喜んで頂いているため、苦労して対応をして良かったです。
資料ダウンロード
この事例で使用した
ソリューション
ソリューション
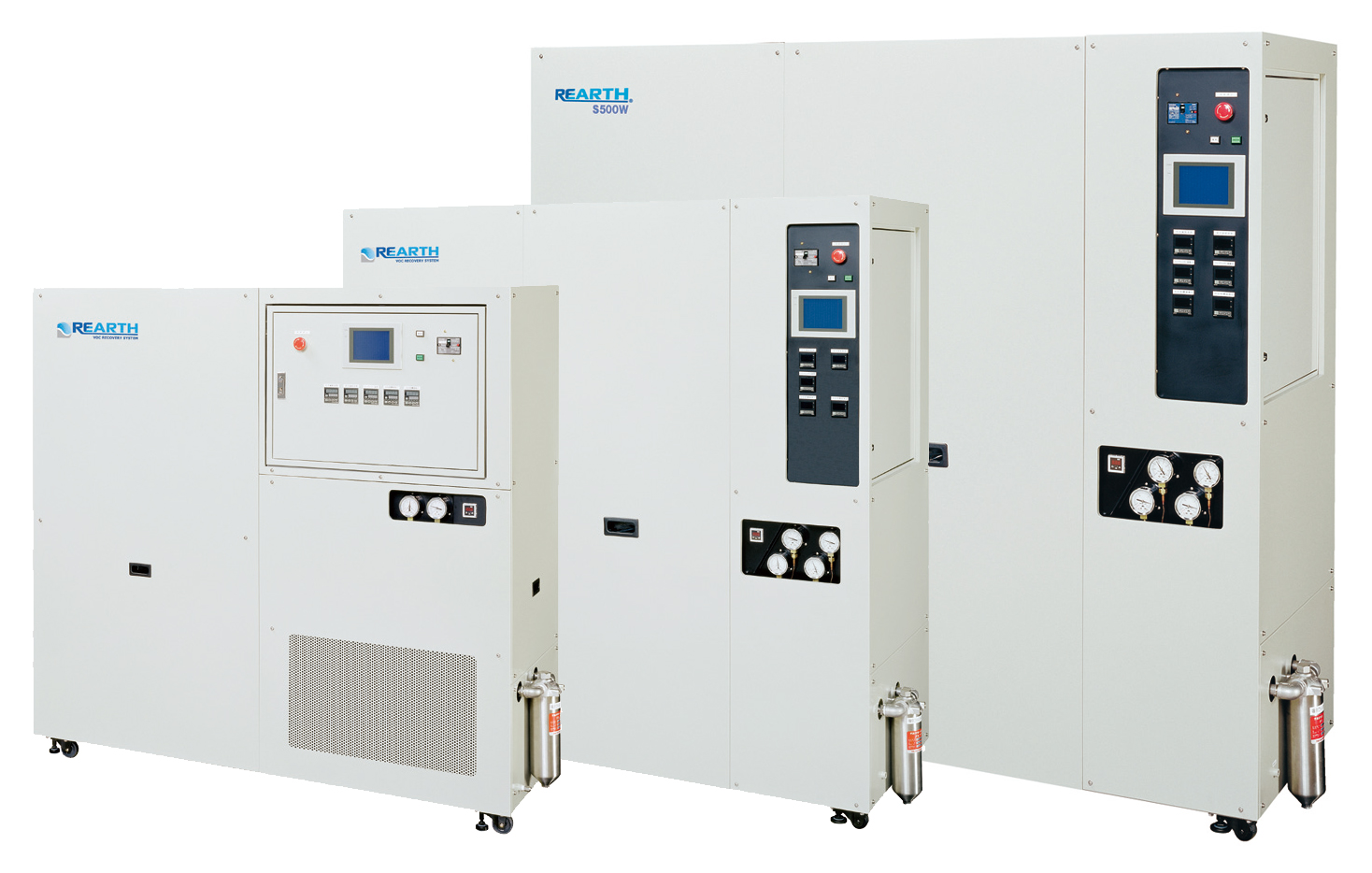
この事例で使用した
ソリューション
ソリューション
株式会社モリカワ
REARTH®️
独自の圧縮深冷凝縮方式により、吸引した高価な有機溶剤ガスを99%以上液化回収します。
精密部品などの洗浄やコーティング等で使用されている有機溶剤ガスを、圧縮冷却して液化し、それを回収することができます。工場や大気中に排出している高価な有機溶剤を再利用することで、溶剤のコスト削減と、環境対策が同時に実現できる製品です。
この事例で提案実施した
コンサルティング
コンサルティング
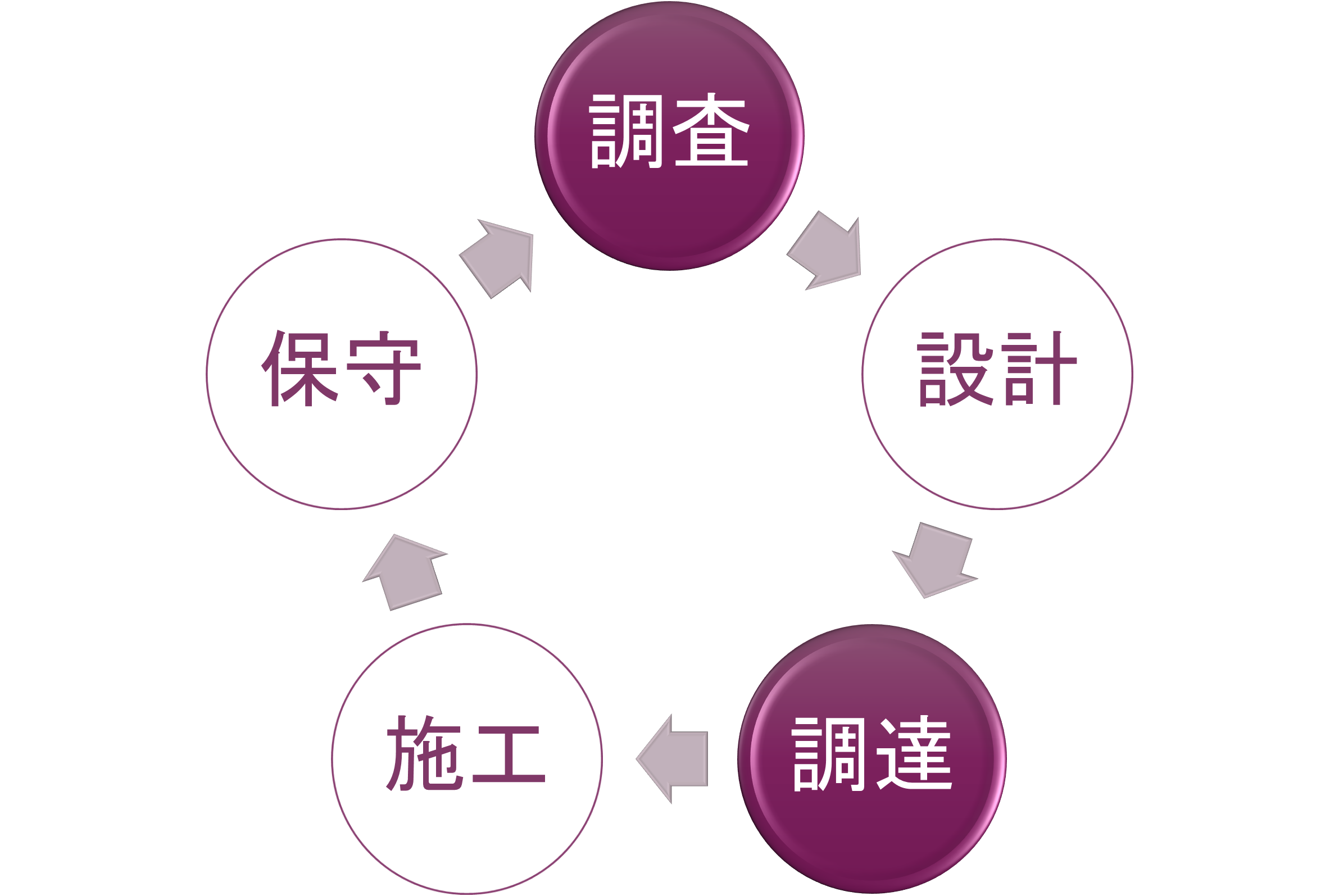
本件に関するお問い合わせ
下のフォームにお問い合わせ内容をご入力いただき、
個人情報の取り扱いに同意のうえ「送信」ボタンを押してください。
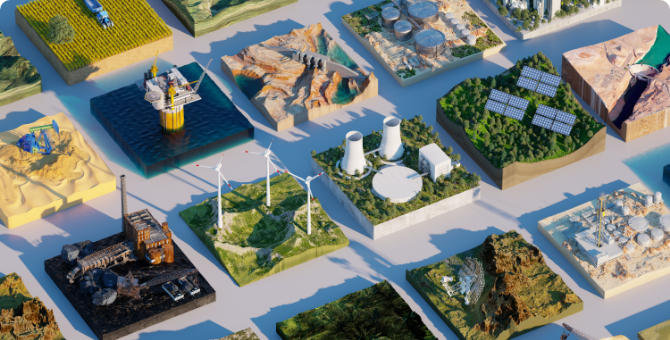
お客さまの課題解決にさまざまなサポートを提供
お問い合わせ