概要
軟質ウレタンフォームの一種
ポリオールとポリイソシアネートを反応させるとウレタン化によって硬化しますが、これに発泡剤を含ませることでフォーム状に硬化させたものがウレタンフォームです。その中でも反応時の気体の発泡量が多く、体積当たりの空隙率が高いものが軟質フォームに分類されます。軟質ウレタンフォームは成形法によって分類することができ、主にスラブ成形とモールド成形の2種類があります。
スラブ成形はコンベア上に原料を流し込み、連続で硬化させることでスラブ(厚板)状のウレタンフォームを得る成形法です。ウレタンフォームは軟らかいため削りにくく、スラブの加工は切断やくり抜きに限られます。そのためスラブ成形は比較的単純な形状のものしか生産できないのがデメリットで、例えば寝具のクッションの生産に使われています。
モールドは「型」という意味です。モールド成形はポリオールなどを含んだ原料混合物を型に流し込んで型ごと加熱硬化させる成形法で、完成品の形状は型の形になります。そのためスラブ成形では生産しにくい曲線形などの複雑な形状のウレタンフォームの生産に使われています。
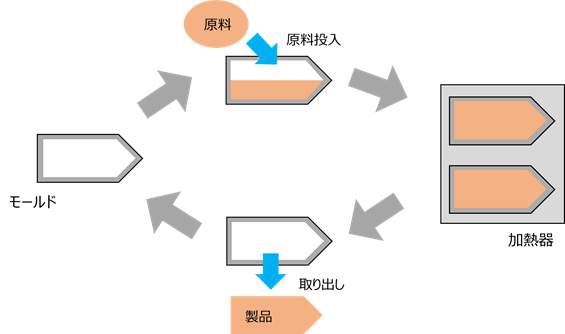
用途
モールド成形は曲線を多用する製品に使われることが多く、例えば座席用のクッションや特殊な建材などに使われます。また、靴底などの比較的小型なウレタンフォームの生産にも使われています。自動車向けのウレタンフォームは家具向けより複雑な形状を要するため、モールド成形が積極的に使われています。
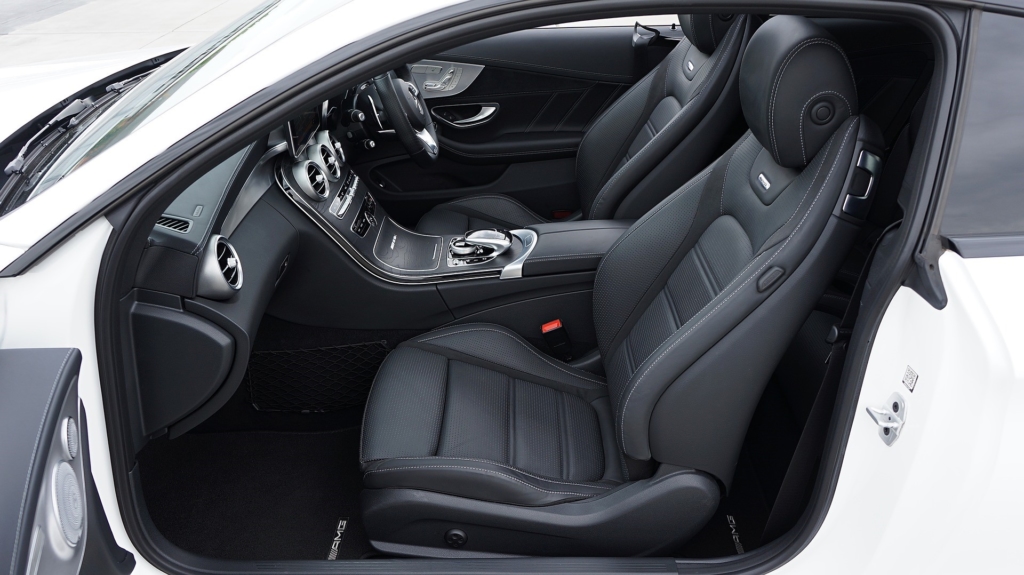
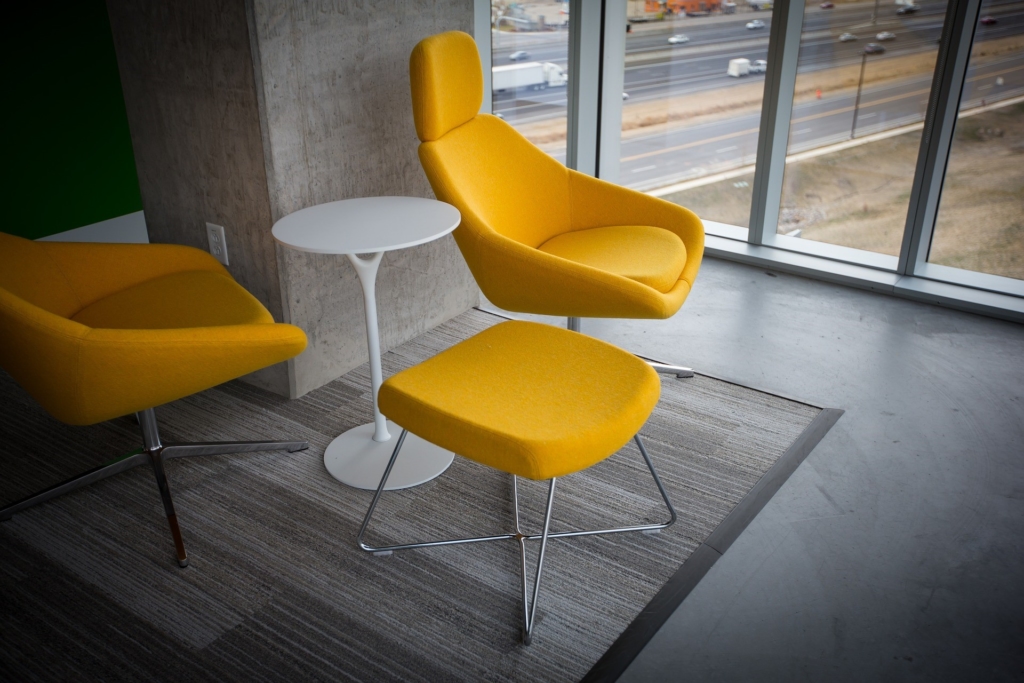
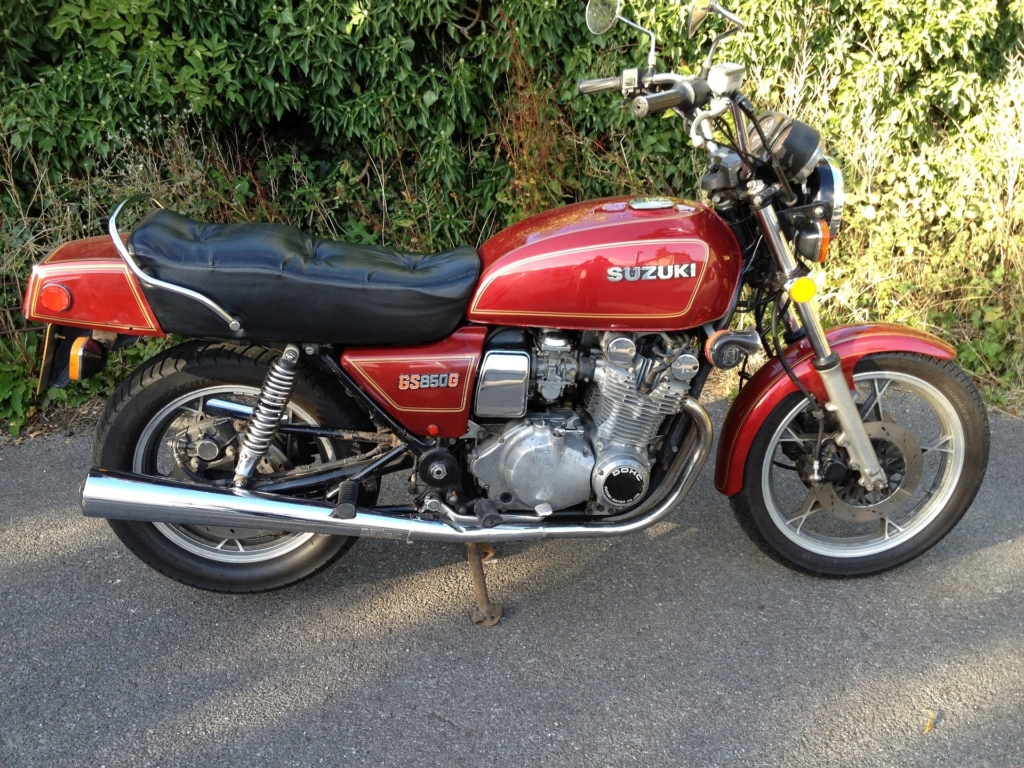
分類
モールド成形は加熱硬化時の温度によってホットキュアとコールドキュアに分類することができます。どちらも①型への原料投入、②型ごと加熱、③型から硬化物を取り出す、という3段階の工程は共通していますが、原料が変わります。ホットキュアは原料混合物の入ったモールドを200±50℃度の加熱炉(オーブン)で加熱し、5~15分前後加熱するのに対し、コールドキュアは100℃前後の加熱炉(オーブン)で成型する方法で、反応(キュア)時間も8分程度です。
原料 | ホットキュアフォーム | コールドキュアフォーム |
---|---|---|
エーテル系ポリオール | 分子量3000~5000 3官能 |
分子量4500~6500 3官能以上 |
イソシアネート | TDI-80 TDI-65 |
TDI-80 TDI-65 TDIぬれーと MDI |
ホットキュアとコールドキュアは使われる原料が多少異なります。コールドキュアはホットキュアよりも反応が進みにくいため、同じ原料を使うと硬化物の分子量が比較的小さく、物性の劣るフォームができてしまいます。これを防ぐためにホットキュアよりも予め分子量の大きいポリオールが使われます。また、官能基数が高いほどゲル化率が高まるため、コールドキュアではホットキュアよりも官能基数の高いポリオールが使われます。官能基の増加は伸び率の低下につながりますが、2官能ポリオールの併用などによって解決する場合があります。
また、ポリイソシアネートの反応性はTDIよりもMDIの方が高く、低温での反応性はMDIの方が優れるためコールドキュアではMDIを併用します。MDI使用のメリットはこれ以外にも、硬度の上昇が早く物性に優れるフォームができる点や、蒸気圧が低いためTDIを単独で使うときよりも揮発するイソシアネート量が少ない点があげられます。一般的にはTDI 70~80%、MDI 20~30%が使用されます。
ホットキュアフォーム
製造法
ホットキュアフォームの大まかな流れは、①型への原料注入、②型ごと加熱、③脱型、④型の清掃です。型への原料投入では、アルミニウムもしくは鋼板製のモールドを80~90℃?前後までに加熱しておき、室温(15~25℃程度)の原料混合物を投入します。150~250℃のオーブンで10分前後反応(キュア)させて、脱型を行います。脱型時の型温は90~110℃になっています。のこのとき取り出したウレタンフォームはバリなどが発生しているため、ブラッシング等によってバリを除きます。その後、空いた型は清掃され離型剤を塗布して再度使われます。
物性
ホットキュアはモールドキュアよりも系内の反応が均一に起こりやすいため、構造が均一なフォームができます。密度はコールドキュアフォームより低く、密度によって硬度が大きく変化します。また、伸び率はコールドキュアフォームより高くなります。耐湿性や耐熱性があり耐久性の優れるフォームができやすいのも特徴です。
経済性、問題点
ホットキュアはコールドキュアのように低温硬化用の原料・触媒を多用する必要が無く、安価な原料を使うことができます。コールドキュアでは欠かせないクラッシング工程(後述)が不要な点もメリットです。しかし設備面では高温を要するため、環境的な側面および作業者の労働条件も厳しいといわれており、日本を含め世界的にも減っていると言われております。
原料 | 配合量 |
---|---|
ポリエーテルポリオール | 100 |
ポリイソシアネート(TDI-80など) | 100~110 |
触媒(アミン類、スズ触媒) | 0.1~0.6 |
水(発泡剤) | 3.0~5.0 |
物性 | 数値 |
---|---|
引張強度 | 100~150(kN/m²) |
伸び率 | 150~250(%) |
オーバーオール部密度 | 30~45(kg/m³) |
コア部密度 | 25~34(kg/m³) |
弾性率 | 33~49(%) |
65%圧縮強さ | 5.5~7.2(kN/m²) |
コールドキュアフォーム
製造法
ホットキュアフォーム同様に①型への原料注入、②型ごと加熱、③脱型、④型の清掃という工程は同じですが、オーブンの温度は90~100℃前後、反応(キュア)時間は10分未満で、温度と時間共にホットキュアより低くなります。また、コールドキュアではクラッシング工程が必要です。クラッシングはフォームを圧縮させることでフォーム内に残った気泡を破裂させる工程で、発泡後のシュリンク防止のために施されます。
物性
コールドキュアフォームはホットキュアフォームよりも密度が高く、反発性が強くなる傾向にあります。伸び率は低くなりますが、力を加えてから除去した後の形状回復が早いという性質を持ちます。そのため座席のシートなどはコールドキュアフォームが使われています。
異硬度モールドフォーム
椅子の座り心地改善のためにはクッション内の位置によって硬度が異なる必要があります。これには硬度の異なる複数のウレタンフォームを使い、部品の場所によって硬度を変える手段が一般的ですが、コールドキュアではMDIを配合するため、モールド内の注入場所を変えることで異硬度フォームが可能になります。
原料 | 配合量 |
---|---|
ポリエーテルポリオール | 100 |
ポリイソシアネート(TDI-80など) | 100~110 |
触媒(アミン類、スズ触媒) | 1.0前後 |
水(発泡剤) | 2.0~3.5 |
物性 | 数値 |
---|---|
引張強度 | 1.3~1.9(kg/cm²) |
オーバーオール部密度 | 43~70(kg/m³) |
コア部密度 | 34~58(kg/m³) |
弾性率 | 60~73(%) |
65%圧縮強さ | 54~102(kg/314cm²) |
まとめ
モールド成形は複雑な形状や小型のフォームを成形するのに適した成形法です。加熱条件によってホットキュアとコールドキュアに分類され、それぞれ違う原料が使われているため異なる物性の完成品がつくられます。
ホットキュア | コールドキュア | |
---|---|---|
製造面 | 高温での加熱が必要 均一なフォームだがバリが出やすい |
低温だが原料が比較的高価 クラッシング工程を要する 異硬度フォームに適応可能 |
物性面 | 硬度-密度が相関している 荷重に対して強い 伸び率が大きい |
高反発性(⇒自動車用シートに) 応力をの座いた後の回復が早い |
原料面 | 高温のため触媒量は少量で十分 特殊原料を必要としない |
密度が高いため、水(発泡剤)は少量で良い 低温硬化用原料が必要 硬化促進のため架橋剤を配合 |